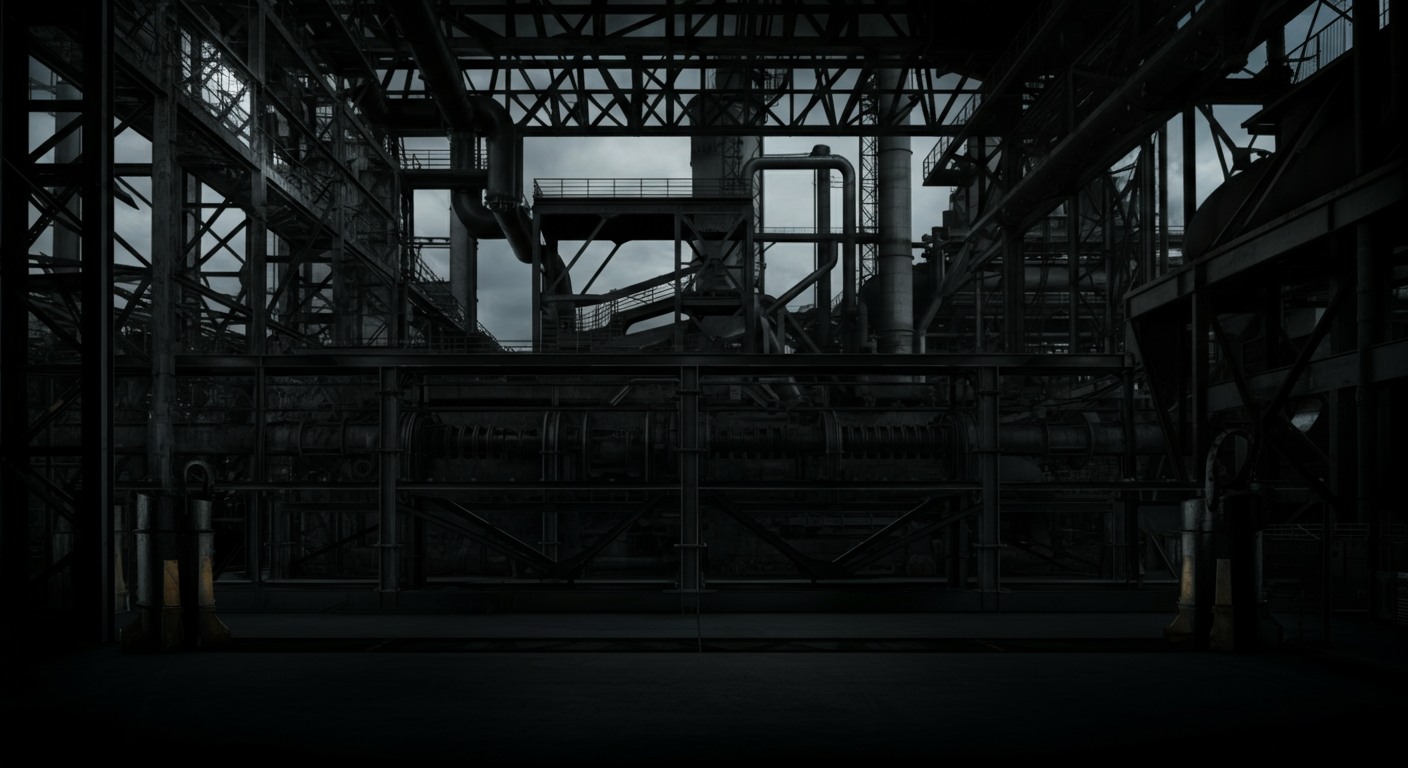
mining and metals
gain control over your site’s lubrication
Eliminate unplanned downtime caused by grease related failures
Unplanned downtime in mining and metals is catastrophic — costing millions in lost production, repair, and recovery. Yet lubrication, one of the leading causes of preventable equipment failure, remains largely invisible.
GreaseBoss gives maintenance teams control in these high-stakes environments, providing the visibility they need to eliminate guesswork from lubrication. Our system turns grease activity into reliable data, enabling prescriptive maintenance, with more targeted shutdowns and smarter maintenance planning. With skilled labour becoming harder to find, GreaseBoss helps crews do more with less — standardising greasing, simplifying verification, and delivering immediate insights that drive uptime, safety, and performance.
reduce bearing failures
by 50%
SKF data reveals that 50% of bearing failures are caused by incorrect lubrication.
GreaseBoss ensures each point receives:
The right grease. In the right amount. At the right time.
eliminate premature
pin & bush failures
CAT identifies under-greasing as the number one cause of pin and bush failures. GreaseBoss ensures critical assets like excavators, loaders, and haul trucks are greased correctly — preventing premature wear and eliminating costly unplanned downtime.
Ensure critical assets
are greased correctly
Ever wondered how much grease auto lubricators are actually delivering to your critical grease points?
Verify the exact volume of grease delivered every pump cycle and receive alerts if your asset is at risk.
Reduce exposure
to high staff turnover
Streamline your manual lubrication, enabling workers to accurately follow the lubrication schedule across your plant with basic training, becoming fully operational within 2 weeks of starting on site.
Fixed or mobile? We’ve got you covered
Harsh environments demand robust, reliable performance. Get the basics right and get the most from your machines.
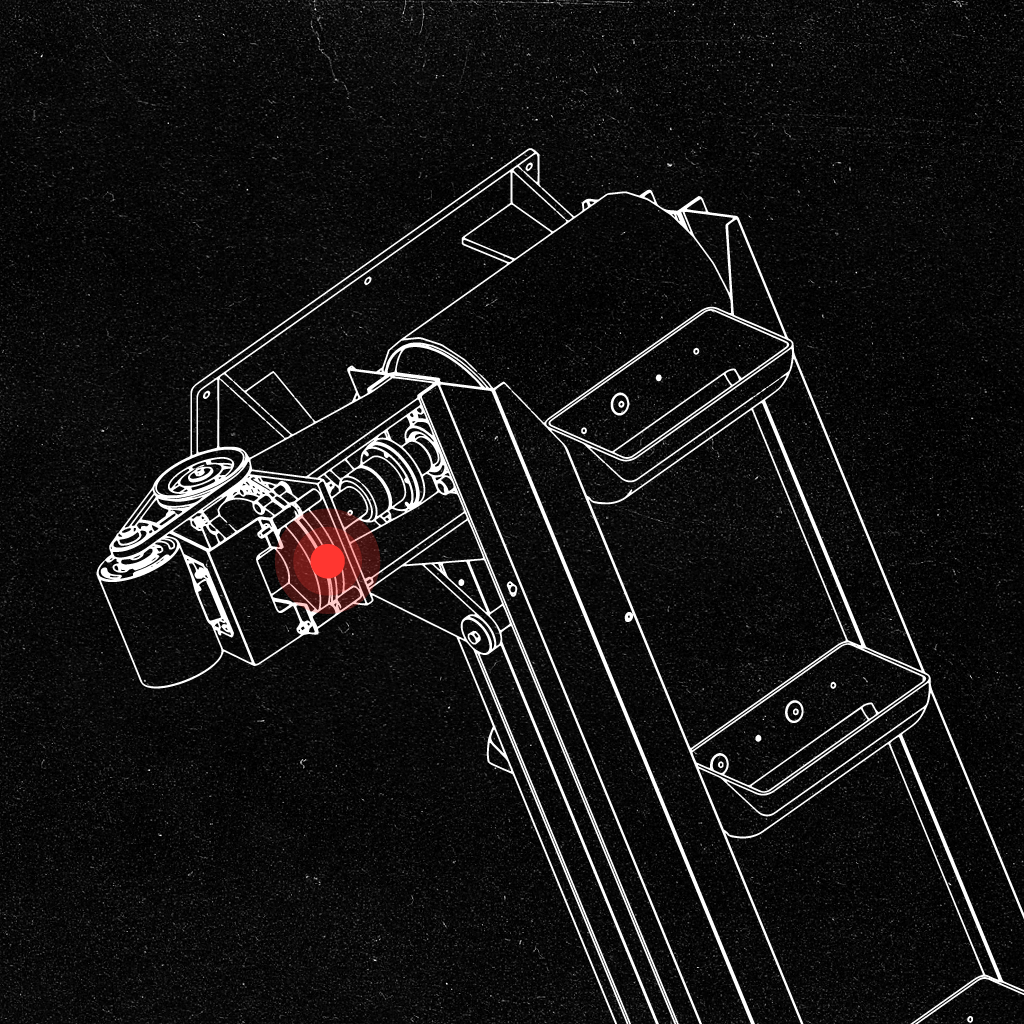
Solutions
FixeD PLANT
Fixed plants contain a mix of equipment, each that have different lubrication needs. Generally, fixed plants require a lubrication strategy that combines both manual and automatic lubrication and traditionally it has been impossible for maintenance managers to verify that equipment is being greased correctly.
The GreaseBoss system provides solutions to monitor both manual and automatic lubrication, providing maintenance managers and their teams with full visibility over their plant’s lubrication, ensuring that every grease point receives the right grease, in the right amount, at the right time.
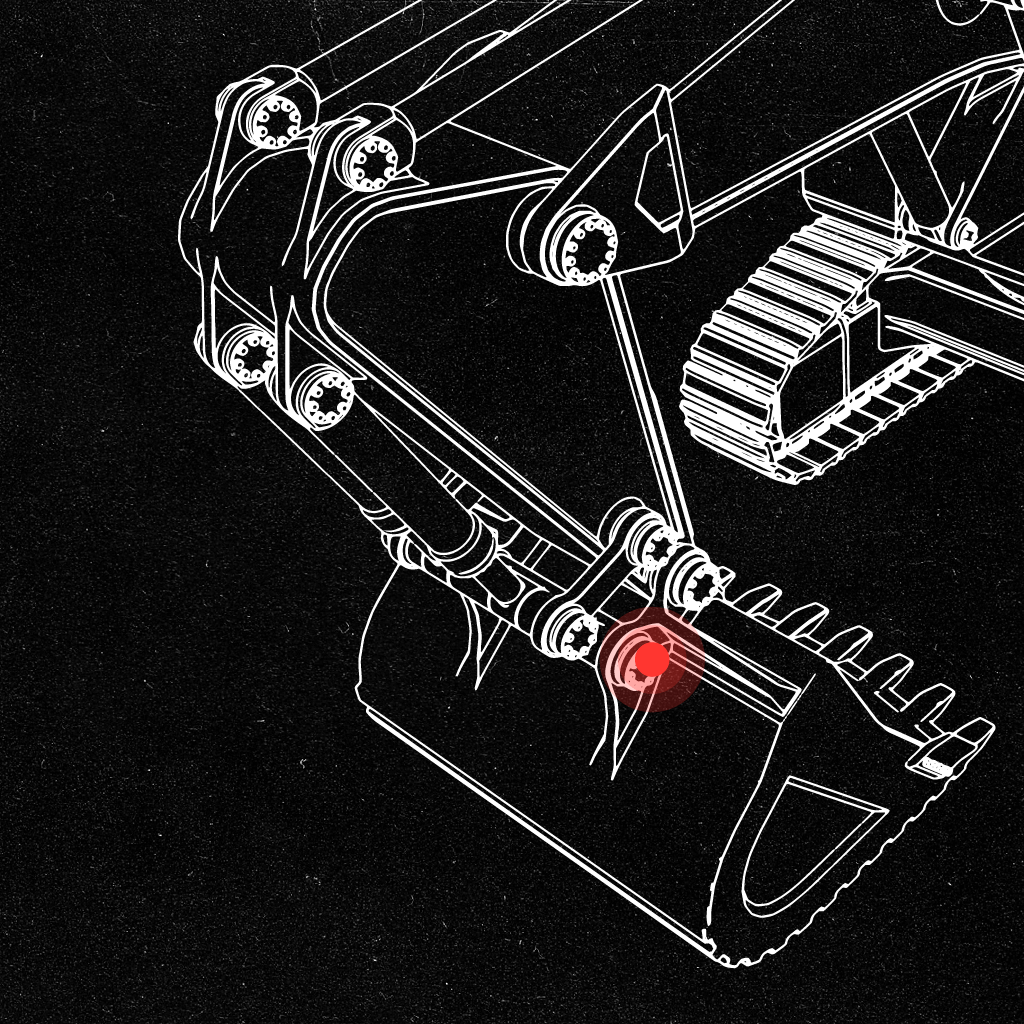
Solutions
HEAVY MOBILE EQUIPMENT
Huge loads, high impact, vibration and dust expose heavy mobile equipment to extreme operating conditions. Reliable and regular grease application is critical for preventing pin and bush failures in these harsh conditions. However, these HME automatic lubrication systems often experience sudden component failures of injectors, distributors and pumps which go unnoticed, leading to undergreasing and equipment failure.
The GreaseBoss HME Solutions provide HME fleet managers with visibility and certainty that their critical assets are being correctly greased to maximise uptime and productivity.
Proven in the Toughest Conditions.
Trusted by the Best.
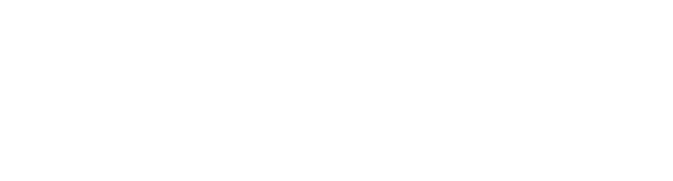
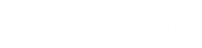
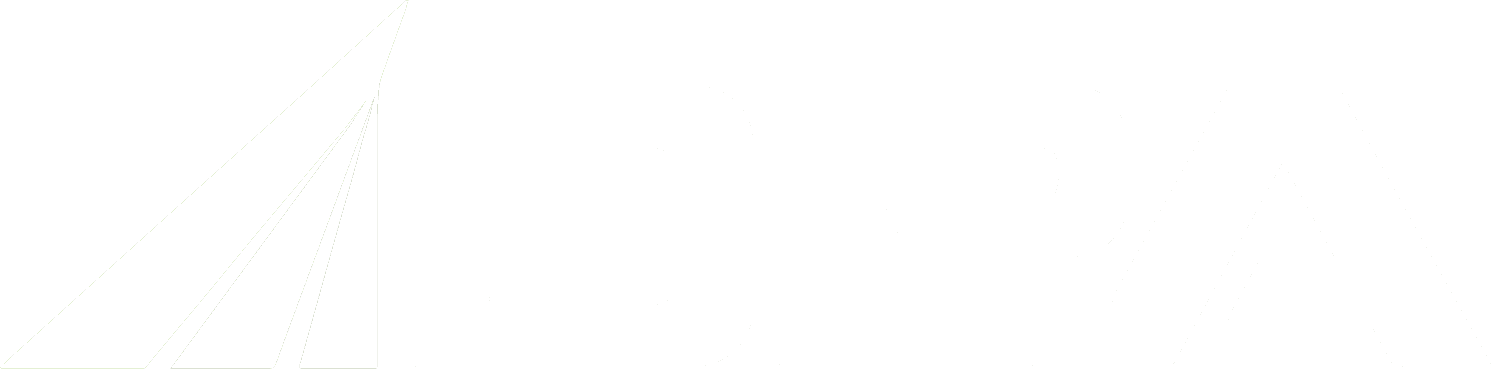