the value of cpm
key benefits
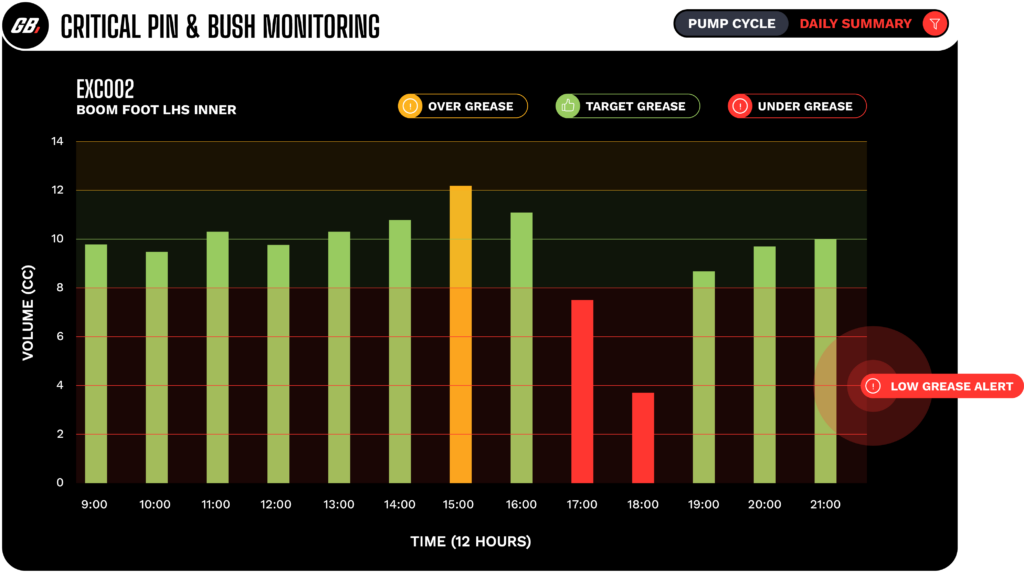
Ensure critical pins and bushes receive the correct grease volume
Verify planned vs actual grease delivery – every pump cycle
The Critical Point Monitoring system conducts a digital balloon test with every pump cycle, verifying that automatic lubricators are performing and critical grease points are receiving the correct grease amount. This visibility enables autolube systems to be set and tuned to meet OEM requirements, with certainty.
Set and forget alerting ensures that when auto lube components such as pumps, injectors, distributors and hoses fail, your maintenance team is notified in near real-time to plan prescriptive maintenance.
Detect blown hoses in high impact areas
Never have a blown hose fail a bucket pin
Installed downstream of injectors and distribtuors, the Endpoint MP2 monitors grease volume, temperature and grease line pressure. In addition to grease volume alerts, monitoring the grease line pressure enables the system to detect if a downstream hose has been blown and trigger alerts to maintenance teams.
This additional monitoring is perfect for high impact areas such as bucket pins or areas where physical inspection is difficult such as slew bearings.
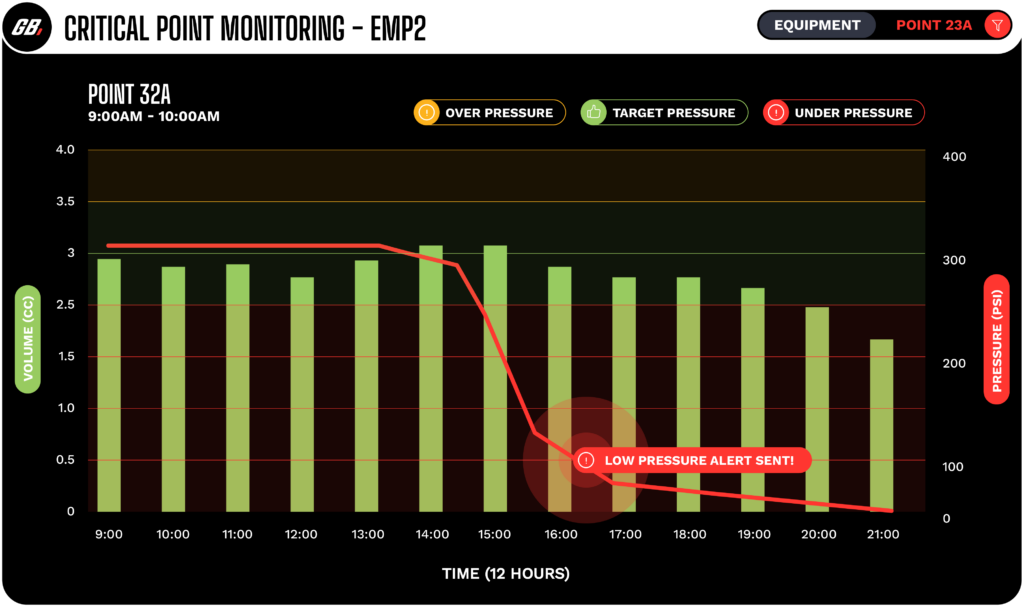
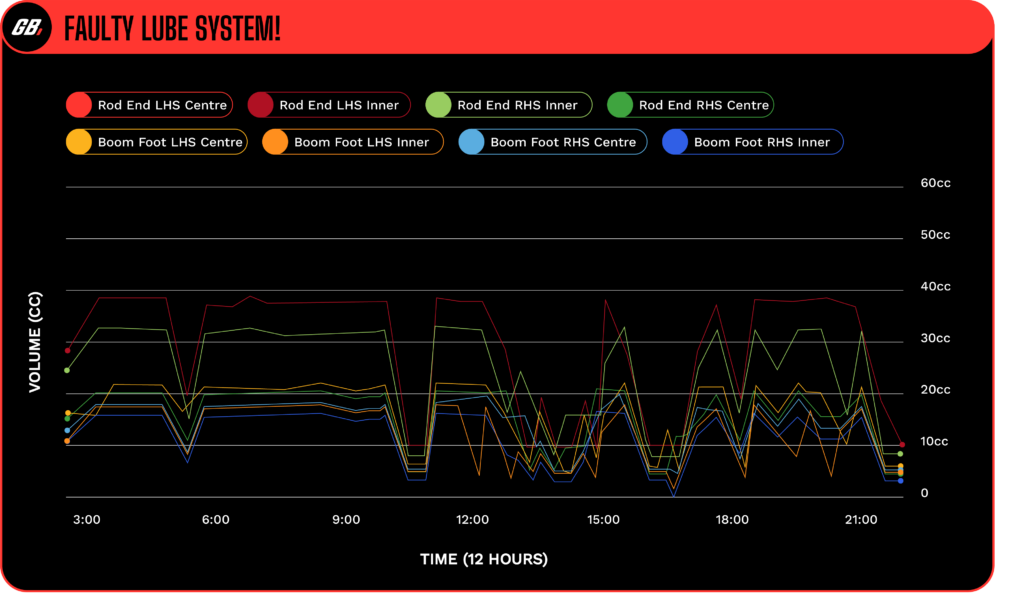
Monitor overall autolube system health
Detect failures in the autolube system and the impact on critical points
When multiple critical points within one automatic lubrication system are monitored, a regular, coherent pattern of grease delivery volume is evident. Failures within the broader lubrication system, such as a bypassing injector on a non-critical point, have major effects across the entire system performance. The Critical Point Monitoring solution can detect these abnormal, chaotic patterns to identify system issues, allowing maintenance teams to schedule automatic lubrication system maintenance.
how this solution works
how it works
The Endpoints record the exact volume of grease that passes through them when the automatic lubrication pump fires. This data is periodically synced (typically every hour) to the nearby Gateway, via Bluetooth.
The Gateway syncs with all Endpoints in the vicinity (typical range is between 50m – 250m, depending on the environment). This Endpoint data is synced to the GreaseBoss Cloud via the configured network backhaul (typically 4G/LTE SIM, site wifi or site OT network).
The Greaseboss Cloud compares the planned vs actual greasing and triggers automatic alerts to maintenance teams if there is an issue with the automatic lubrication system.
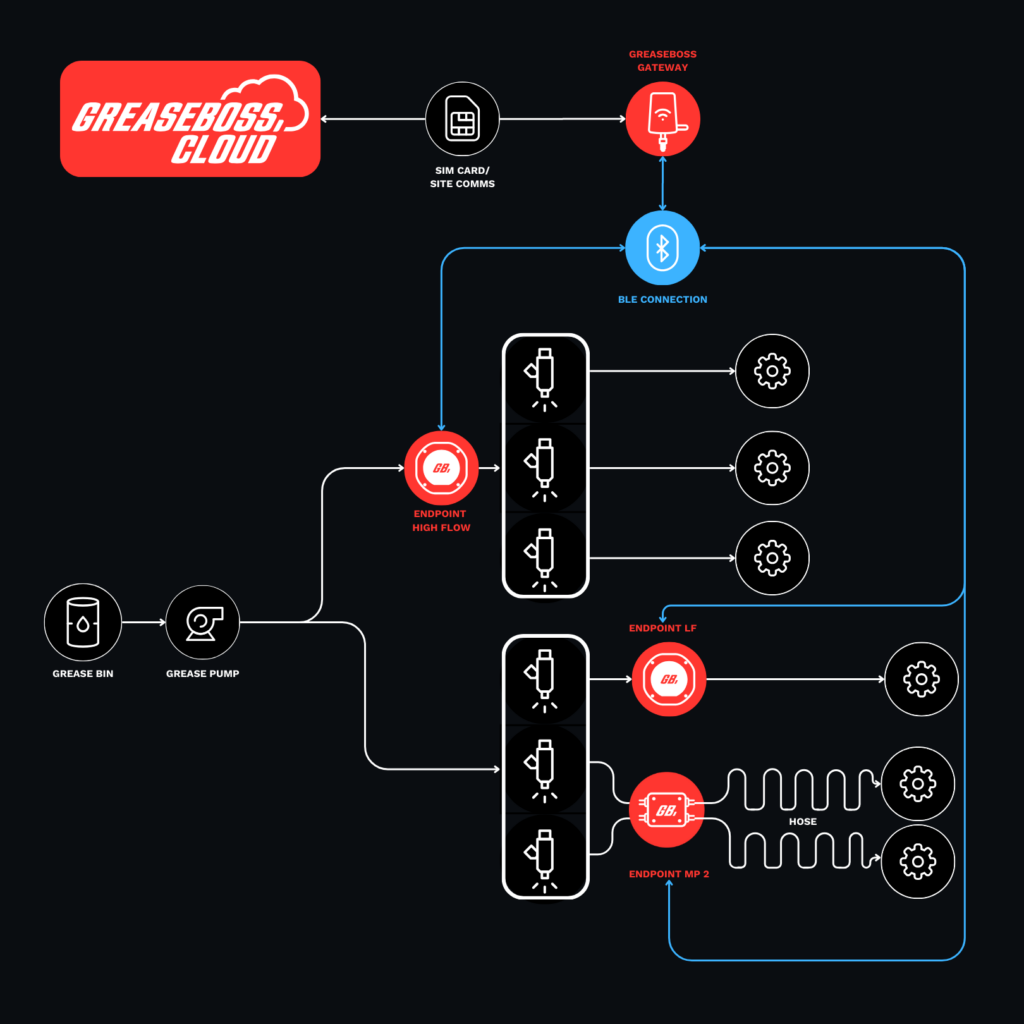
products used
in this solution
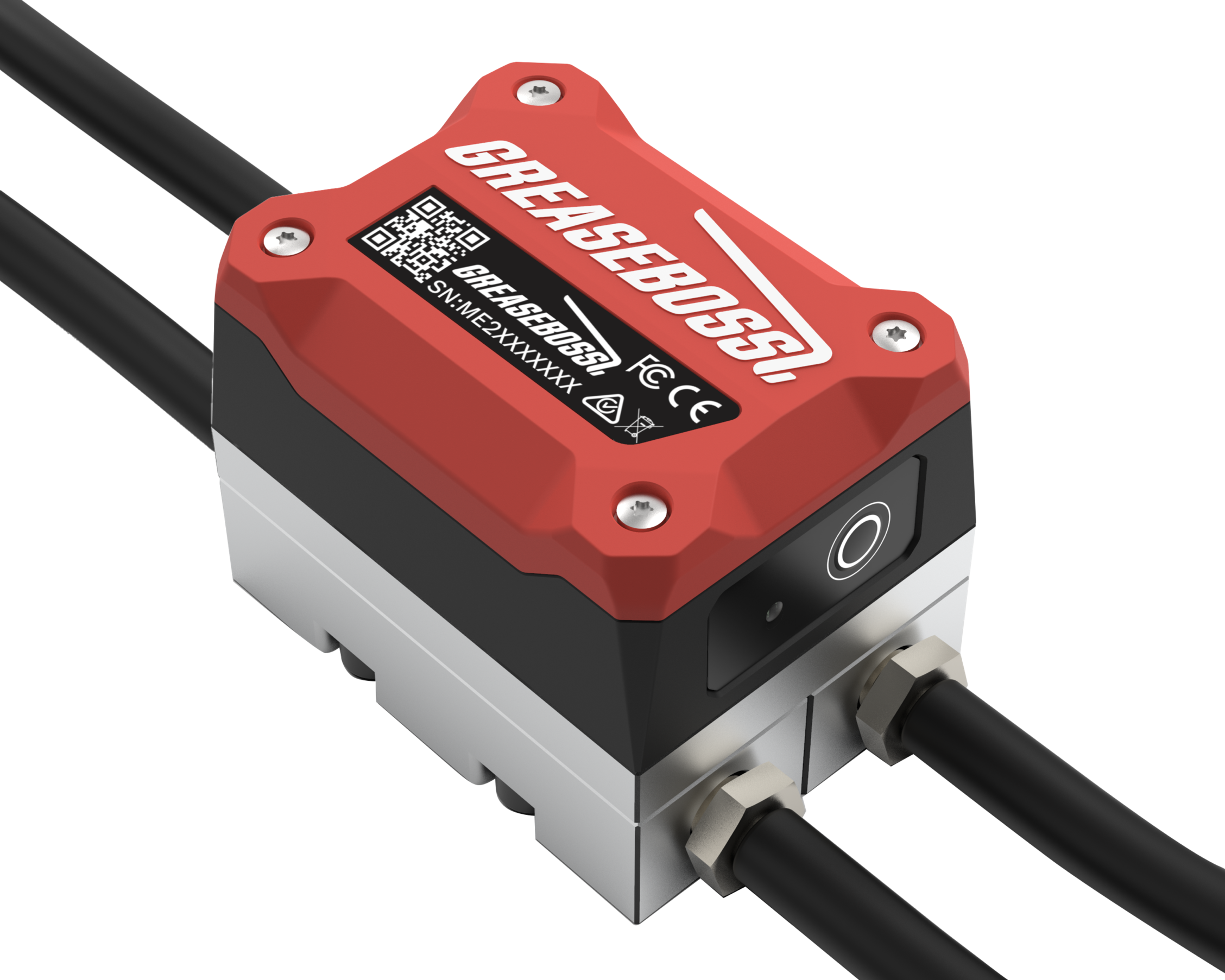
PRODUCT
Endpoint MP2
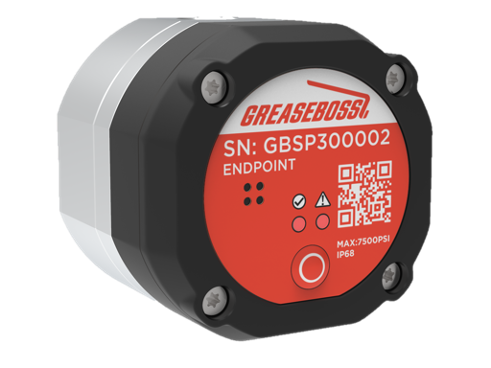
PRODUCT
Endpoint LF/HF
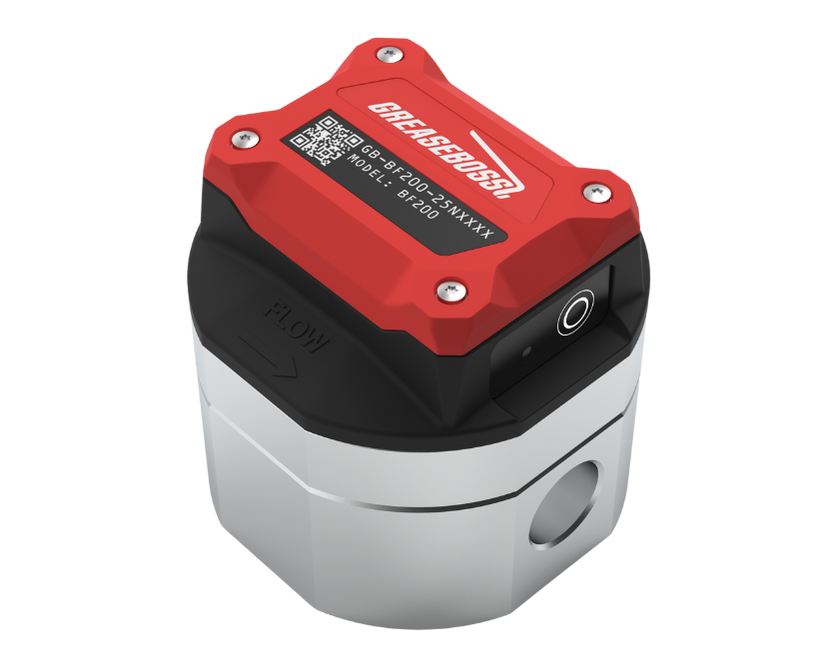
PRODUCT
Endpoint BF
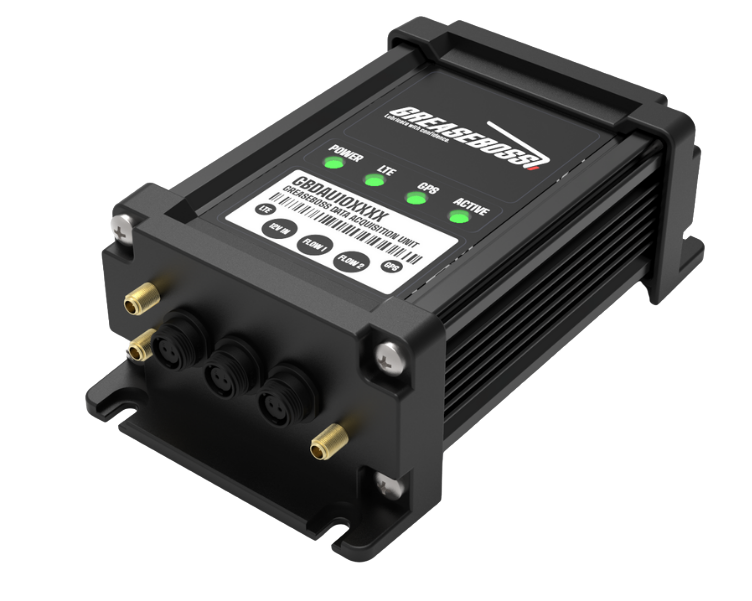
PRODUCT
HME Gateway
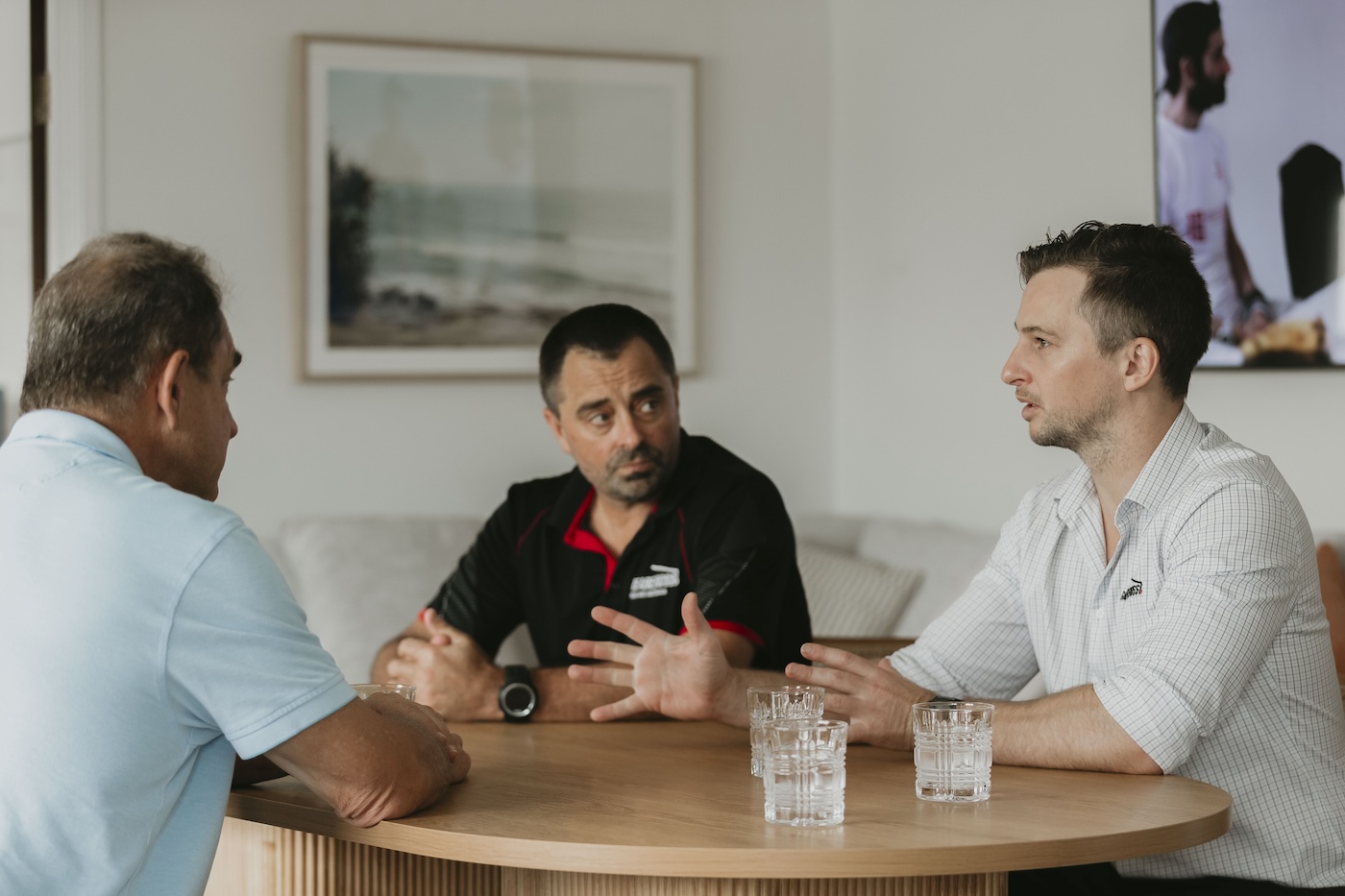
book a demo
OF this solution
"*" indicates required fields
Frequently Asked questions
see our faqs
Our operations are remote. If no access to 4G system are there alternative communication options?
Yes. The Gateway can be configured to use site WI-FI network or connected via LAN directly into the site OT network where the data is processed on an on-site server then forwarded to the GreaseBoss Cloud.
The GreaseBoss team will work with our customers to set up the most suitable backhaul option for client’s requirements.
How does my grease event data get to the GreaseBoss Cloud?
The data is synced from the devices to the Gateway via Bluetooth. The Gateway then forwards data to the GreaseBoss Cloud using the configured connectivity backhaul option.
Can I use my site wi-fi to connect to the GreaseBoss Cloud?
Yes, the GreaseBoss team will work with your site IT/OT team to use existing WI-FI networks to connect to the GreaseBoss Cloud.
Can I install or do I need a qualified GreaseBoss installer?
The system can be easily installed by customers with remote support from the GreaseBoss team but we do offer installation services directly with our Certified GreaseBoss installers to provide high–quality turnkey solutions to our customers.
What training and onboarding do I get from GreaseBoss?
The GreaseBoss onboarding process is comprehensive and assists to set up the correct lubrication data in the GreaseBoss Cloud, and to prepare the site for installation, commissioning, and on-going operations.
GreaseBoss offers comprehensive training to customer teams in the field for installation, commissioning and hardware use, training for the office team on how to use the GreaseBoss Cloud, and how to interpret the reports & alerts.