the value of cpm
key benefits
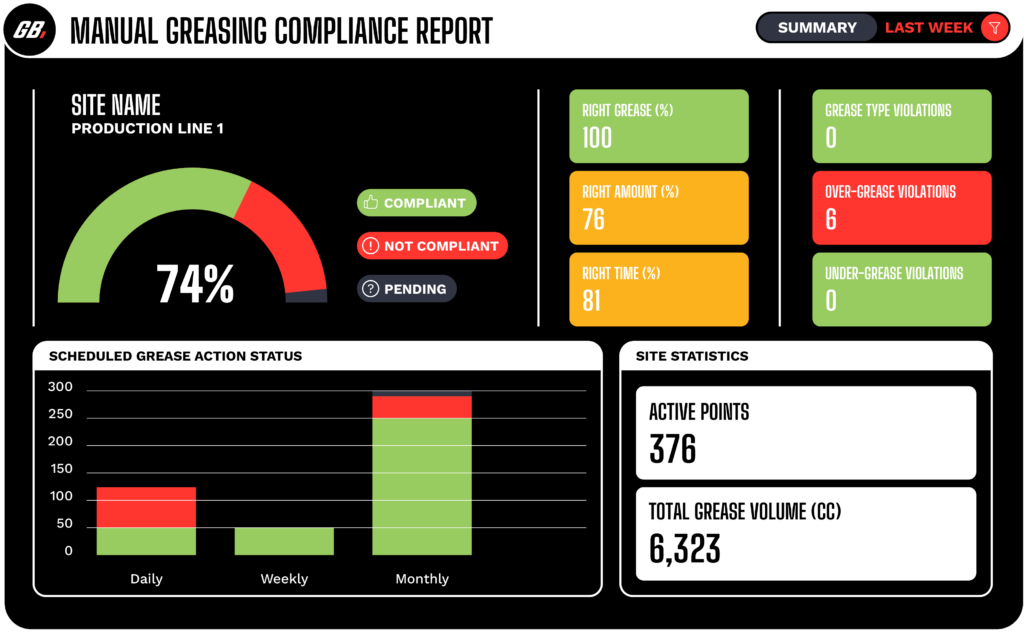
PROVIDE VISIBILITY TO
MAINTENANCE TEAM
PLANNED VS ACTUAL
COMPLIANCE REPORTS
Maintenance managers and their teams gain
clear insights into planned versus actual
greasing activities through simple, insightful
reports.
Managers can ensure that assets are properly
maintained whilst driving continuous
improvement of greasing activities on site.
SYSTEMISE AND
STANDARDISE GREASING
enable workers with minimal training
The GreaseBoss Manual Lubrication System provides clear instructions to lubrication technicians, offering detailed information from the lubrication schedule to guide them through a predetermined grease route.
The system ensures that workers with minimal training can perform greasing accurately and efficiently, safeguarding the operational integrity of your equipment.
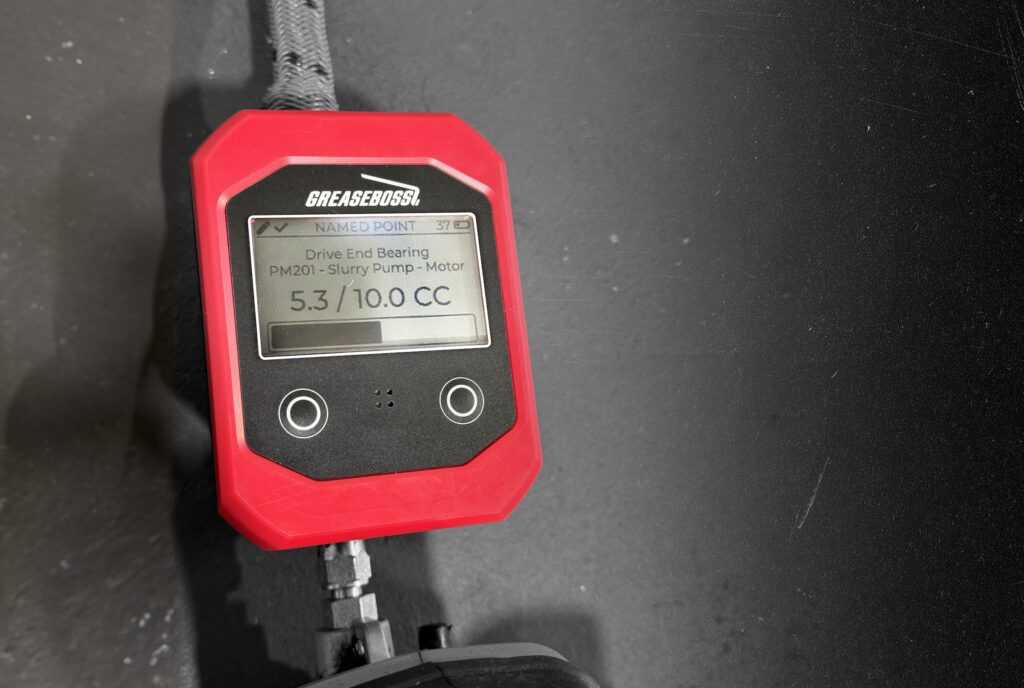
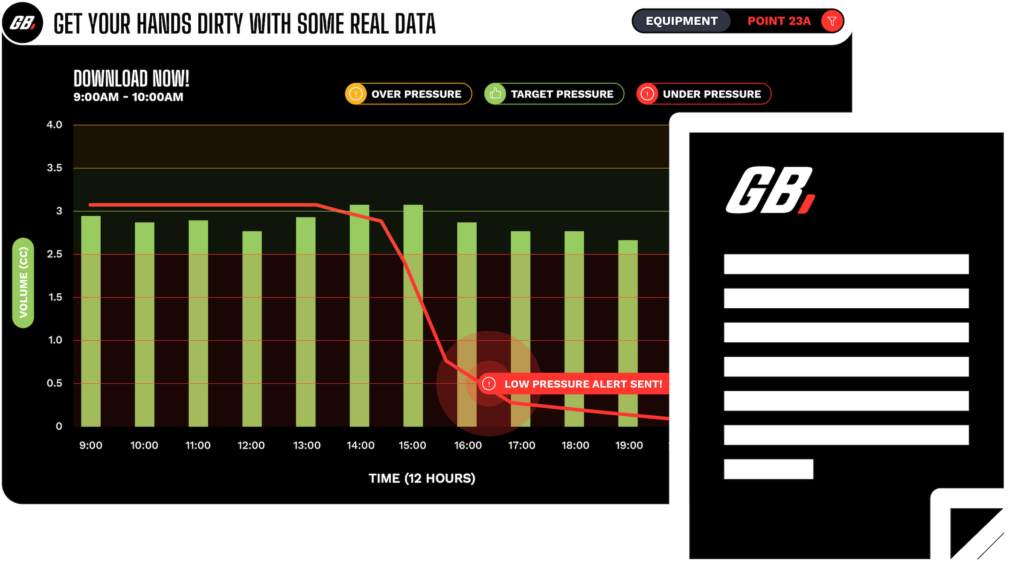
Manual Lubrication
Example
Compliance Report
Review an example of a compliance report summarising the manual greasing performance for the previous week.
This report is automatically emailed to the Maintenance Manager and the team.
manual lubrication
how it works
The GreaseBoss Cloud is configured with the site’s lubrication schedule. The site hierarchy is configured under Locations > Assets > Grease Points.
Each grease point has 3 critical attributes:
1. Grease type required
2. Grease volume required
3. Frequency it must be greased.
On site, GreaseTags are installed on each grease point and the unique RFID code is mapped into GreaseBoss Cloud using the GreaseBoss App (typical install and commission time is 30 seconds for a GreaseTag).
The Head Unit replaces the hose on any grease gun and is configured to a specific grease type.
The GreaseBoss Cloud manages the lubrication schedule to a very high level of detail and syncs this information to the Head Unit, via the Gateway (typically using a 4G/LTE SIM or site wifi).
When the greaser picks up the grease gun, the Head Unit provides simple, intuitive instructions on how to complete the scheduled greasing. Once completed, the Head Unit syncs this data back to the GreaseBoss Cloud for planned vs actual analysis and reporting.
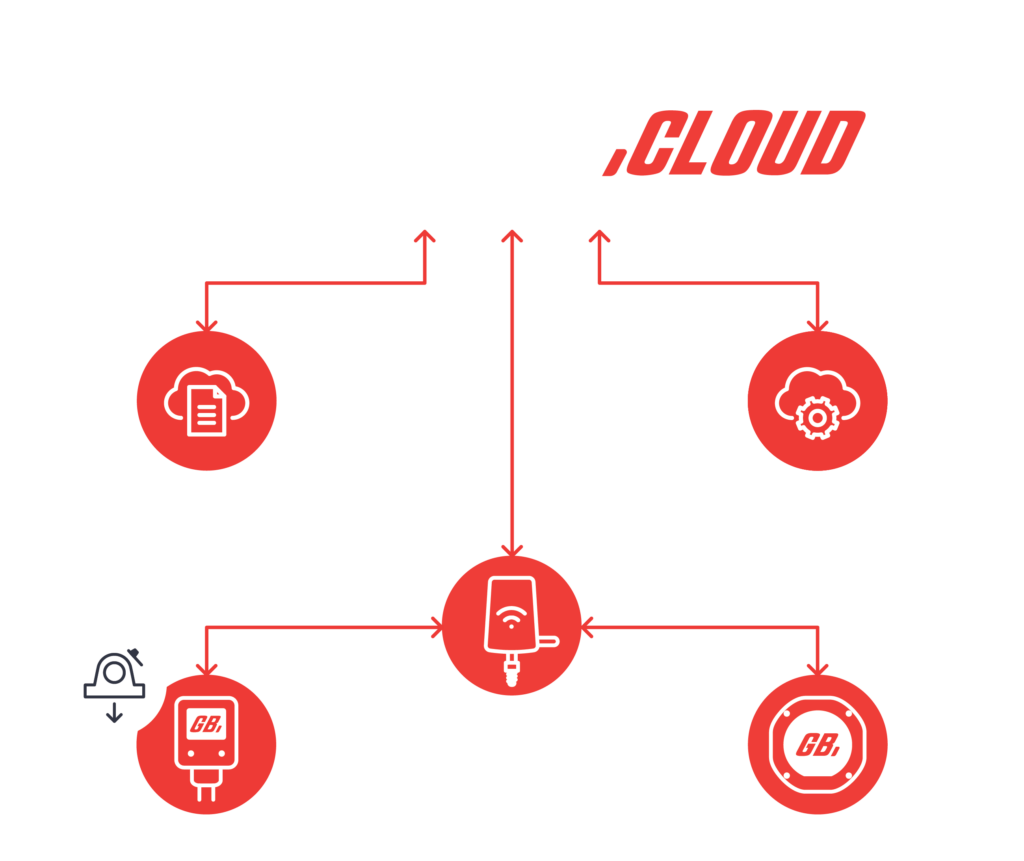
products used
in this solution
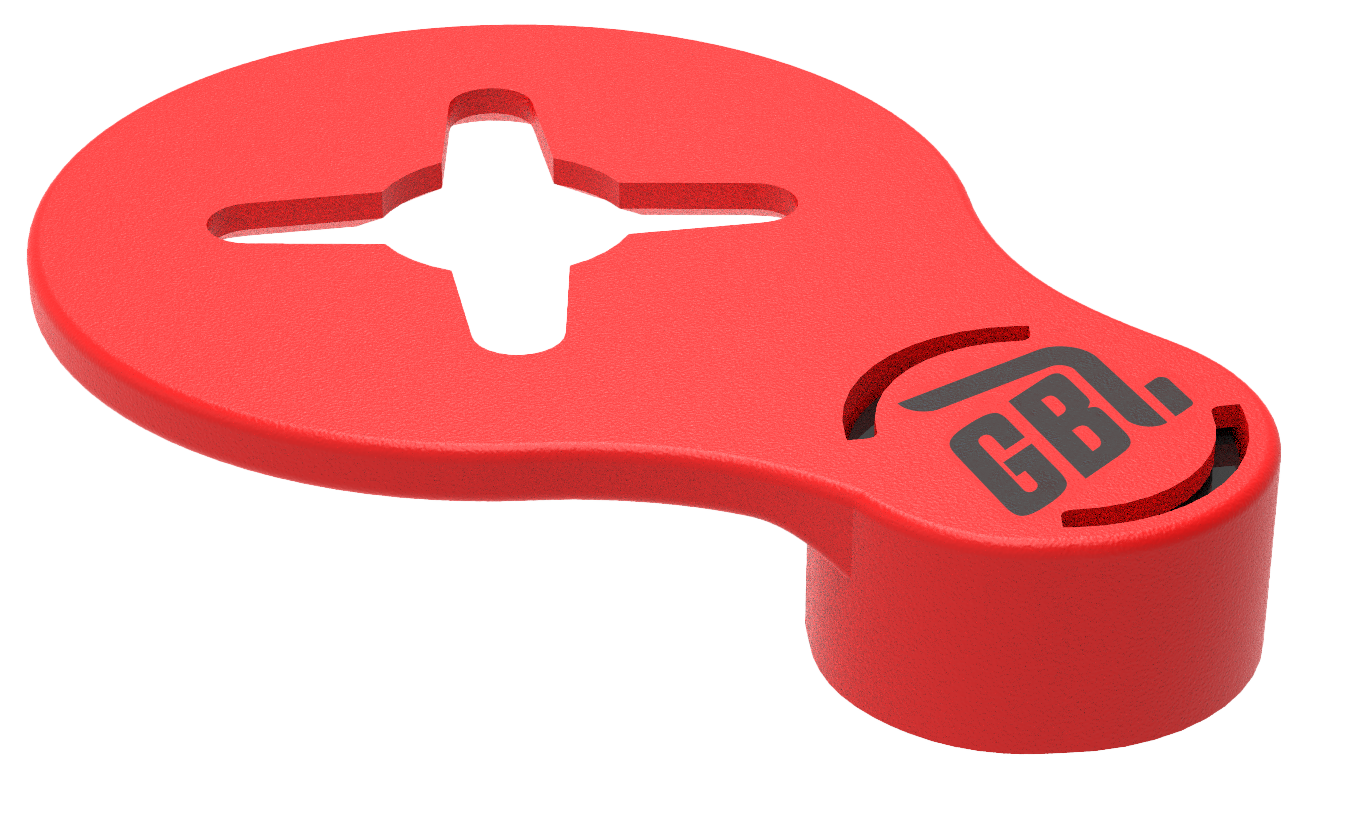
PRODUCT
GreaseTags
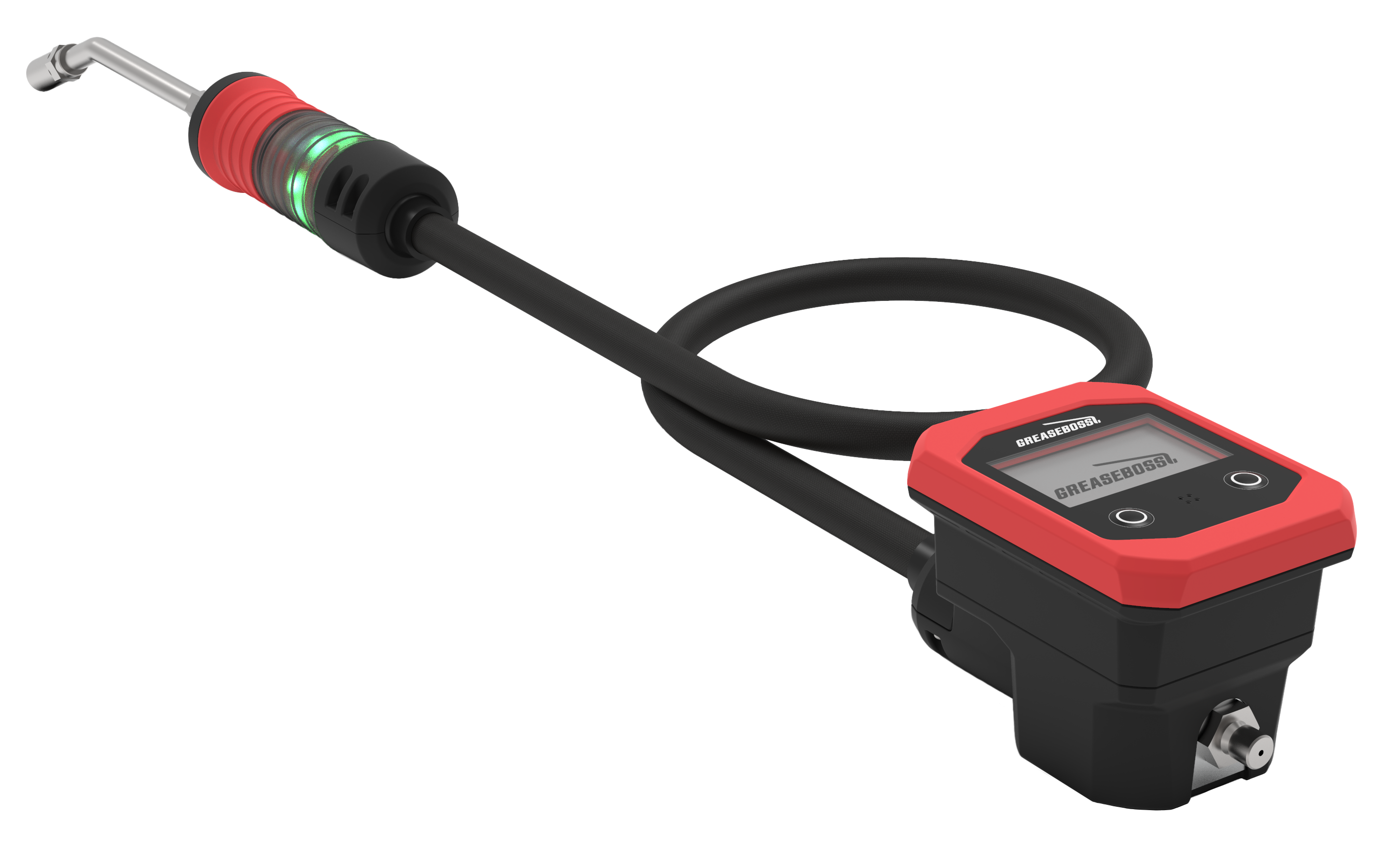
PRODUCT
Head Unit
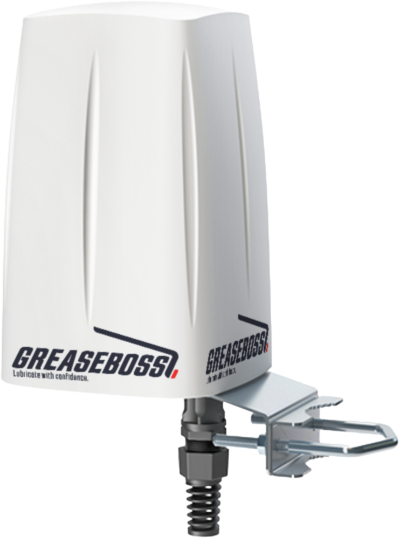
PRODUCT
Gateway
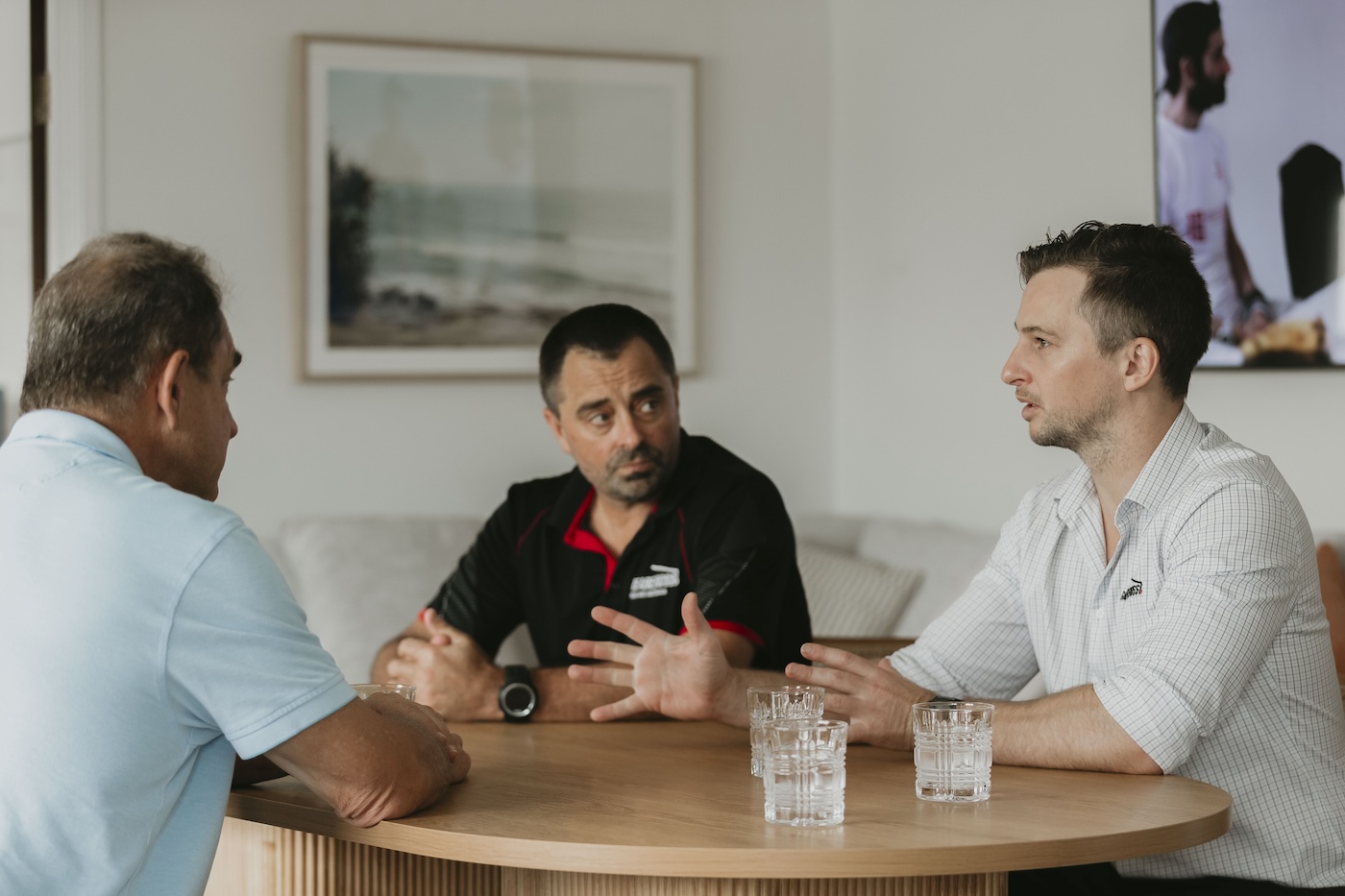
book a demo
OF this solution
"*" indicates required fields
Frequently Asked questions
see our faqs
Our operations are remote. If no access to 4G system are there alternative communication options?
Yes. The Gateway can be configured to use site WI-FI network or connected via LAN directly into the site OT network where the data is processed on an on-site server then forwarded to the GreaseBoss Cloud.
The GreaseBoss team will work with our customers to set up the most suitable backhaul option for client’s requirements.
How does my grease event data get to the GreaseBoss Cloud?
The data is synced from the devices to the Gateway via Bluetooth. The Gateway then forwards data to the GreaseBoss Cloud using the configured connectivity backhaul option.
Can I use my site wi-fi to connect to the GreaseBoss Cloud?
Yes, the GreaseBoss team will work with your site IT/OT team to use existing WI-FI networks to connect to the GreaseBoss Cloud.
Can I install or do I need a qualified GreaseBoss installer?
The system can be easily installed by customers with remote support from the GreaseBoss team but we do offer installation services directly with our Certified GreaseBoss installers to provide high–quality turnkey solutions to our customers.
What training and onboarding do I get from GreaseBoss?
The GreaseBoss onboarding process is comprehensive and assists to set up the correct lubrication data in the GreaseBoss Cloud, and to prepare the site for installation, commissioning, and on-going operations.
GreaseBoss offers comprehensive training to customer teams in the field for installation, commissioning and hardware use, training for the office team on how to use the GreaseBoss Cloud, and how to interpret the reports & alerts.