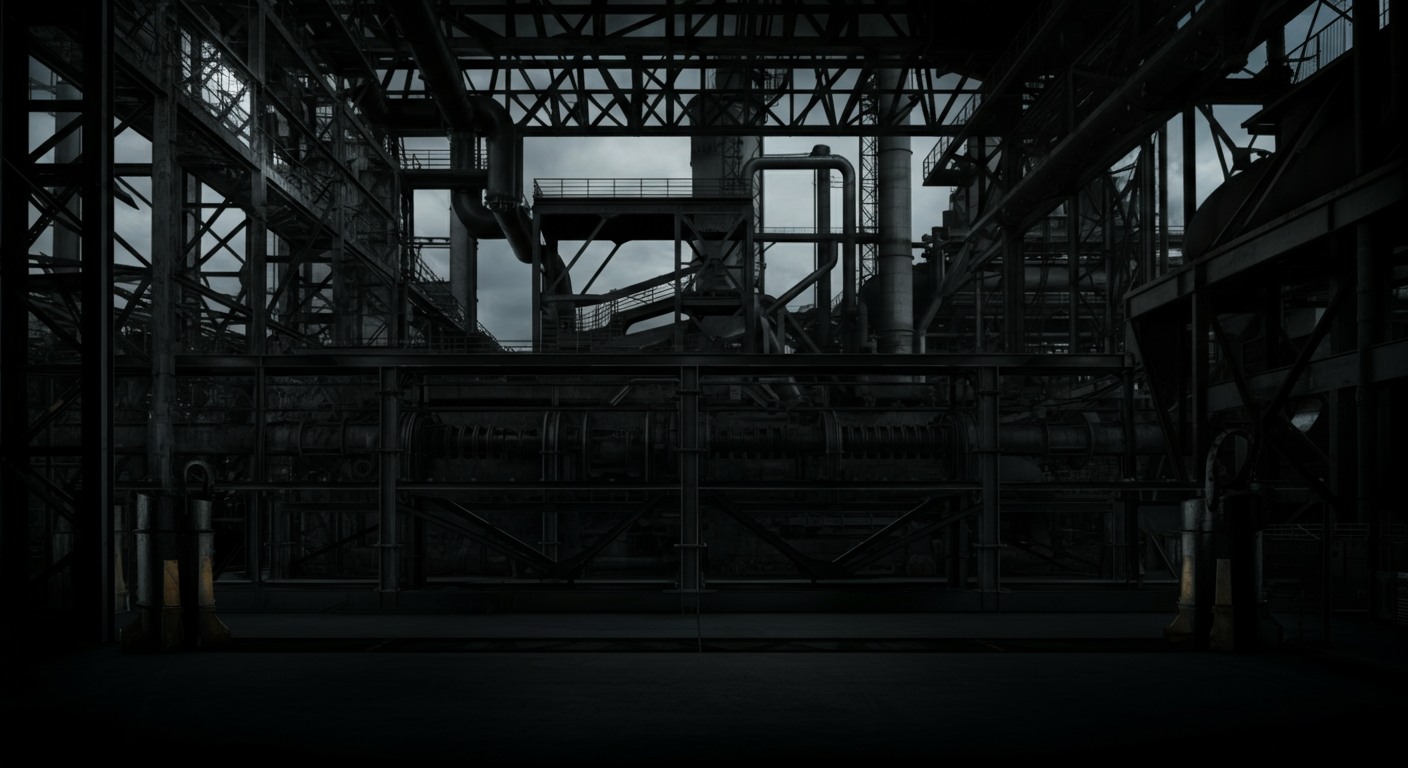
ARTICLES.
-
Noria whitepaper: Monitoring Grease Delivery Where It Counts
Originally posted at https://www.machinerylubrication.com – View Full Article Heavy Mobile Equipment (HME) operates under some of…
-
Pioneering Digital Lubrication Management for Heavy Industry
Originally posted at https://theelitex.com – View Full Article With a background in mechanical engineering and a…
-
The Keys to Eliminating Unplanned Downtime
Originally posted at https://www.machinerylubrication.com – View Full Article It’s been estimated that, globally, unplanned downtime costs…
-
Awards & Recognition
The Fixed-Plant product suite has won numerous Awards and rapidly achieved recognition in the following:
-
Glencore mangoola – SYSTEMISE MANUAL GREASING TO BOOST RELIABILITY
The Mangoola team use external contractors to perform manual lubrication tasks and needed visibility and assurance…