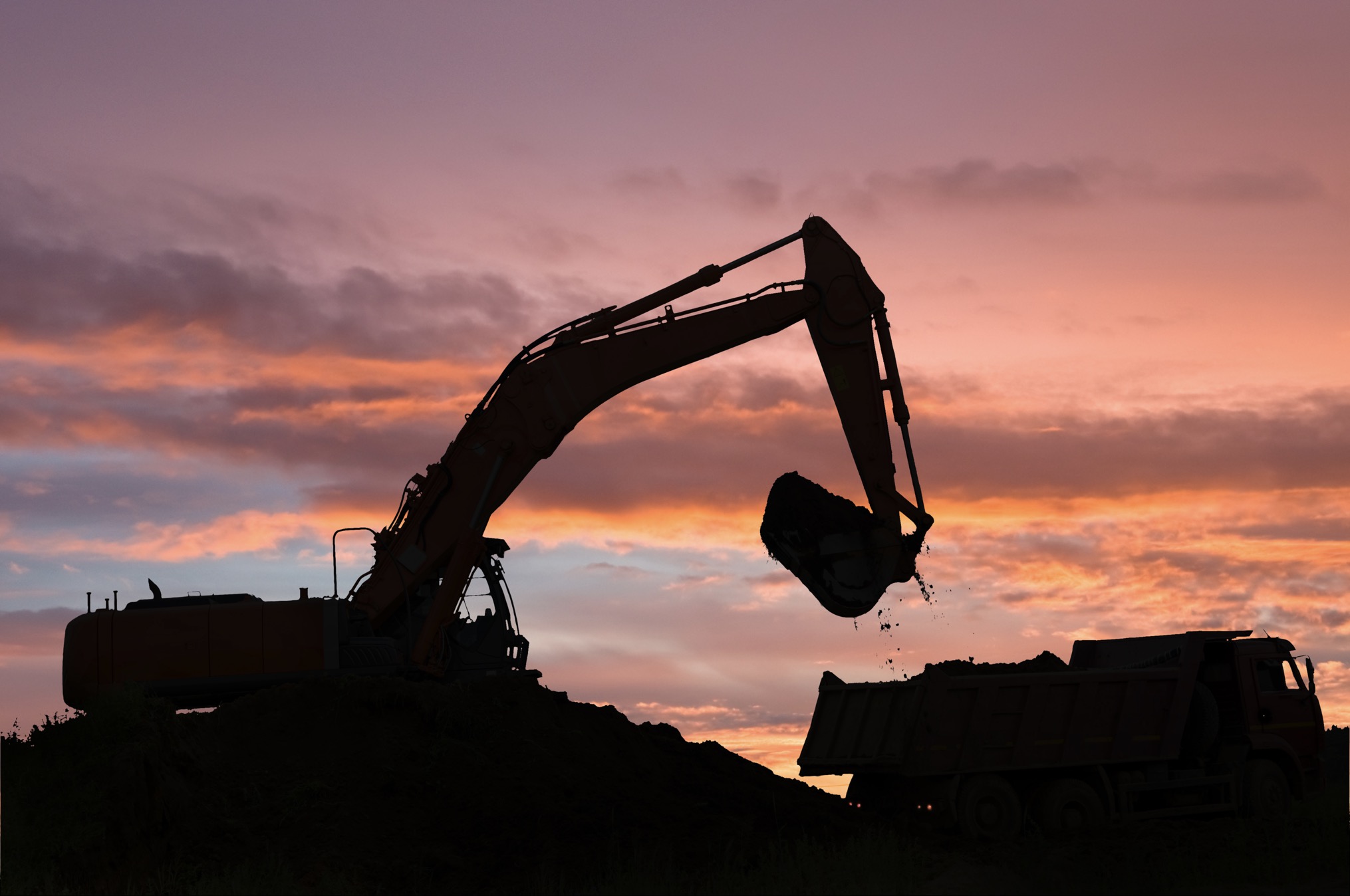
Heavy Mobile Equipment Solutions
THE NEW STANDARD IN GREASE MANAGEMENT
Boost asset availability by eliminating premature pin and bush failures on heavy mobile equipment. CAT identifies insufficient lubrication as the #1 cause of pin and bush failures. The GreaseBoss HME solutions ensure mobile equipment is greased correctly to prevent unplanned downtime and production losses.
komatsu case study video
HEAVY MOBILE EQUIPMENT SOLUTIONS VIDEO
Boost asset availability
Gain control of your fleet’s lubrication
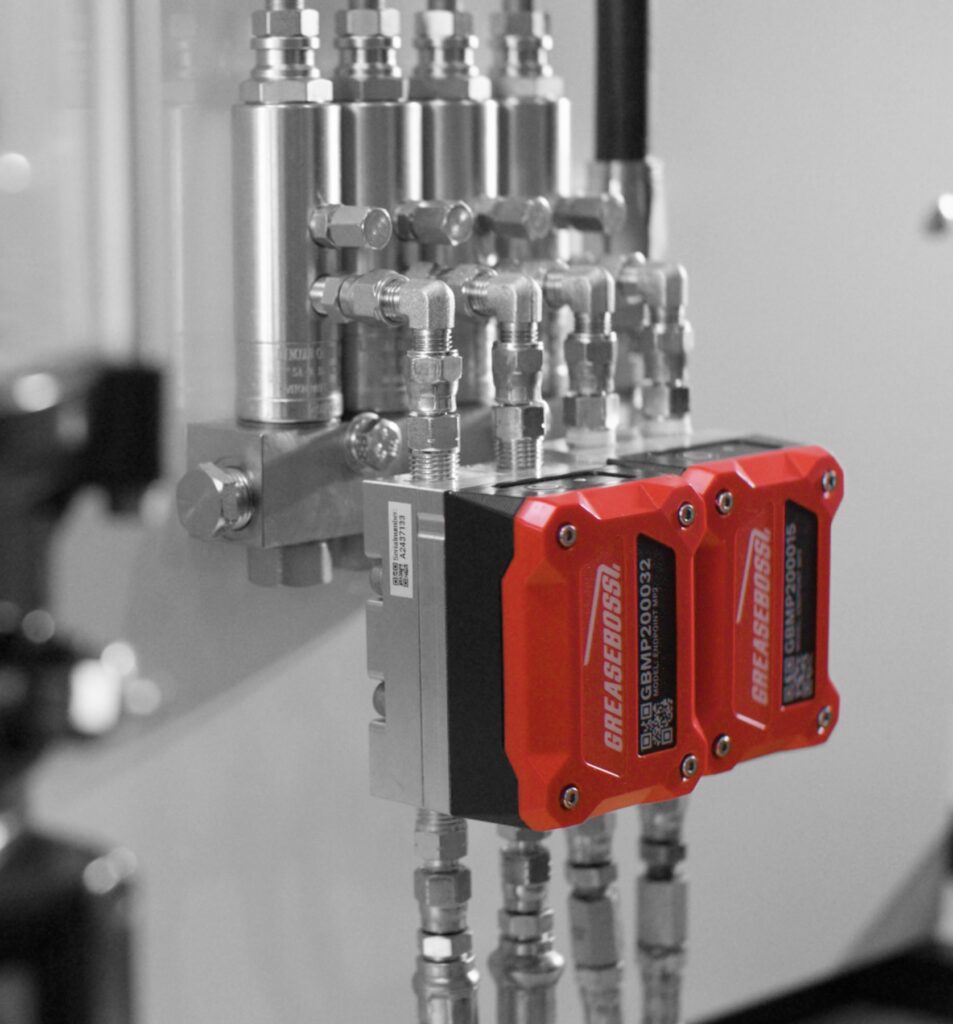
Mobile Equipment
Critical Point Monitoring
Heavy mobile equipment solutions
Verify automatic lubricators are delivering the correct volume.
Heavy mobile equipment experience extreme loading during operation and components can fail catastrophically after only a few hours of no grease.
Automatic lubrication systems on heavy mobile equipment suffer harsh operating conditions and have regular failures of injectors, distributors and pumps. One failed injector can impact the entire lube system’s performance, without triggering traditional automatic lubrication system alarms.
Our Critical Point Monitoring solution verifies the exact volume of grease delivered every pump cycle, and grease line pressure sensing can detect blown hoses in high impact zones. Powerful reporting provides insights into lube system health, and alerts maintenance teams as soon as grease delivery is out of specification. This enables maintenance teams to stop assets before critical components fail and to schedule targeted maintenance during maintenance windows.

Mobile Equipment
Bulk Lubrication Management
Baseline fleet grease consumption against industry standard
Are grease tanks running empty?
How much grease does your fleet consume?
What assets are the biggest grease consumers?
How does your fleet compare to industry benchmarks?
The Bulk Lubrication Management solution provides unparalleled data on the performance of your automatic lubrication systems, as a whole, and enables remote tank level monitoring to ensure your refilling regime is effective. The solution verifies the exact amount of grease pumped to pressurise the auto lube system and the amount of grease flowing back into the tank during venting. Powerful reporting provides insights into pump system health and automatic alerts ensure your maintenance team are notified of failed pumps, failed bypass valves, empty grease tanks and bypassing injectors.
Fleetwide reports on grease consumption per asset highlight outliers that require attention and enable comparison against industry baselines.