Right Grease.
Right Amount.
Right Time.
lubricate with confidence
Eliminate the risk of grease related failures
Visibility over planned vs actual greasing
Prevent critical equipment failures.
Remote visibility of how equipment is being greased.
Automatic alerts enable efficient prescriptive maintenance.
Systemise manual greasing to enable staff with minimal training and safeguard against staff turnover.
GREASEBOSS SYSTEM SUMMARY VIDEO
Fixed or mobile? We’ve got you covered
Harsh environments demand robust, reliable performance.
Get the basics right and get the most from your machines.
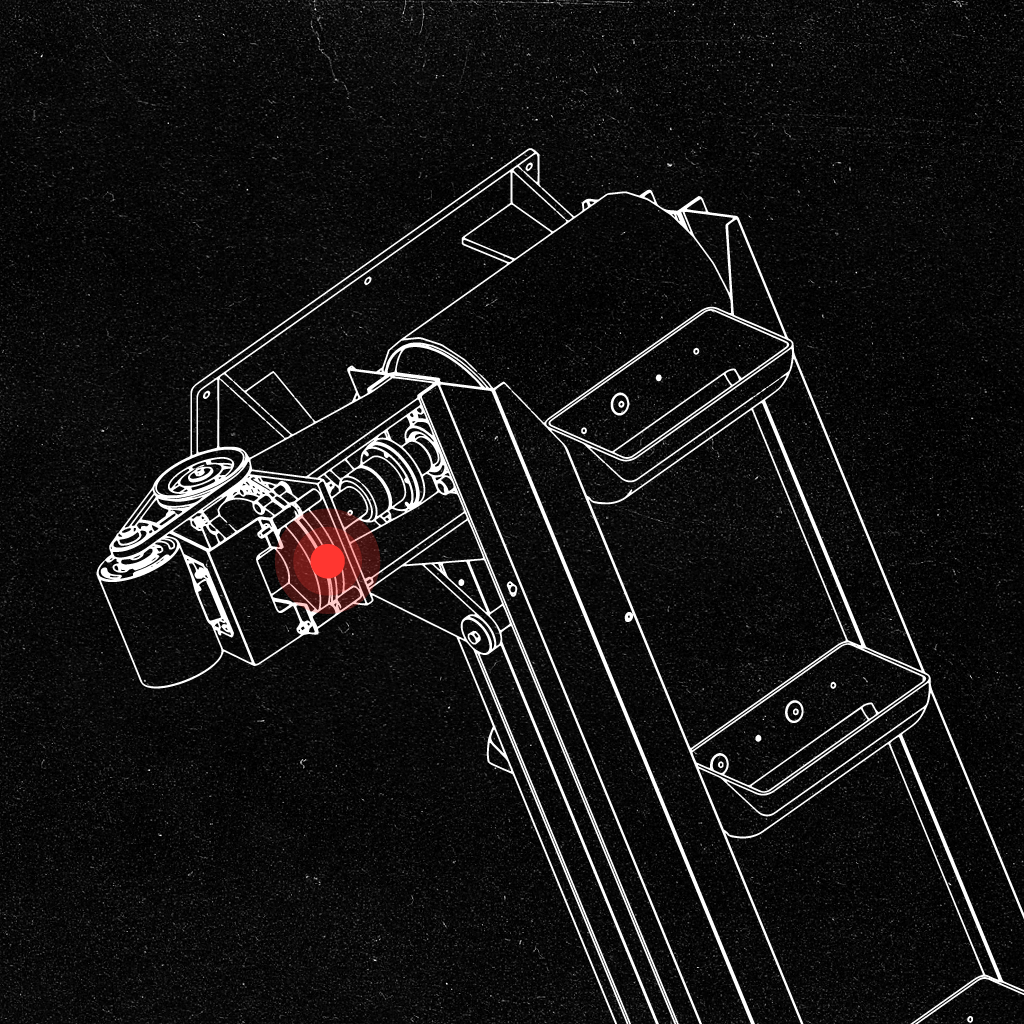
Solutions
FixeD PLANT
Fixed plants contain a mix of equipment, each that have different lubrication needs. Generally, fixed plants require a lubrication strategy that combines both manual and automatic lubrication and traditionally it has been impossible for maintenance managers to verify that equipment is being greased correctly.
The GreaseBoss system provides solutions to monitor both manual and automatic lubrication, providing maintenance managers and their teams with full visibility over their plant’s lubrication, ensuring that every grease point receives the right grease, in the right amount, at the right time.
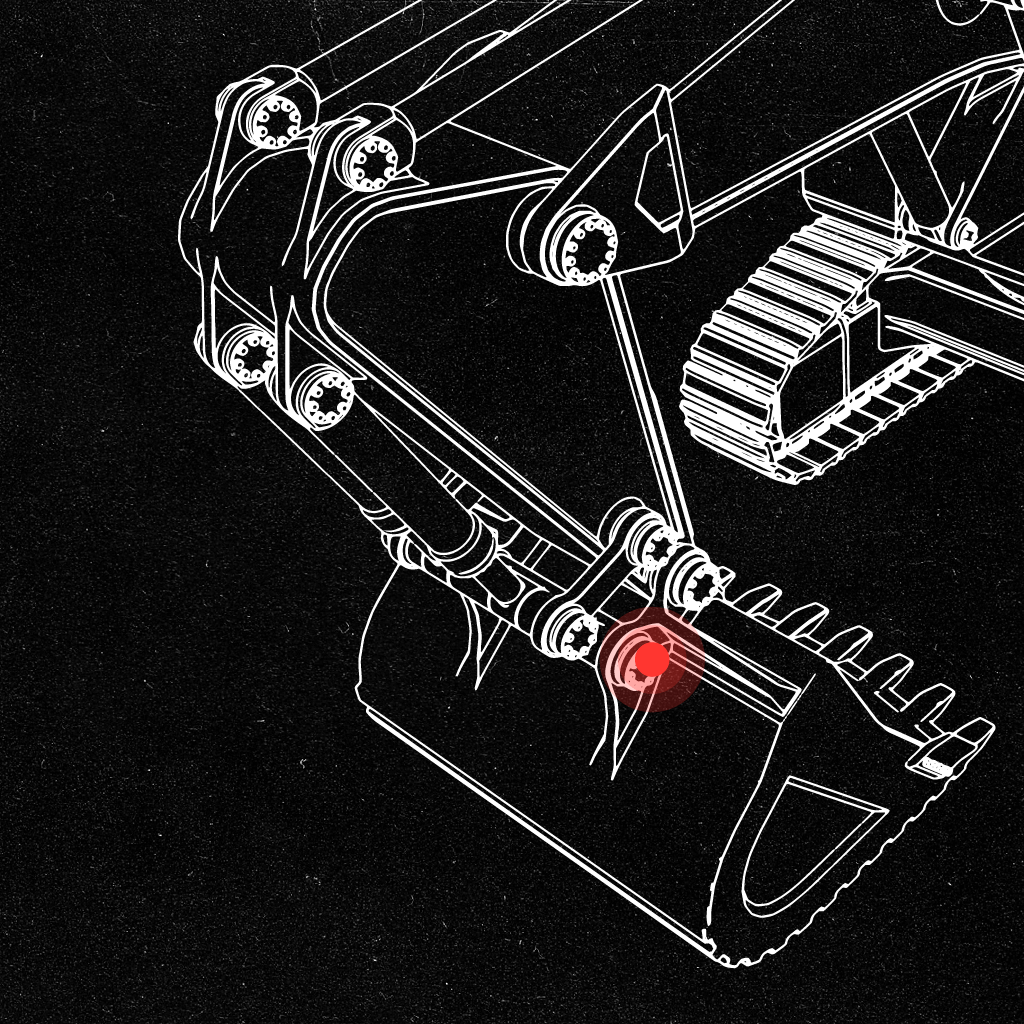
Solutions
HEAVY MOBILE EQUIPMENT
Huge loads, high impact, vibration and dust expose heavy mobile equipment to extreme operating conditions. Reliable and regular grease application is critical for preventing pin and bush failures in these harsh conditions. However, these HME automatic lubrication systems often experience sudden component failures of injectors, distributors and pumps which go unnoticed, leading to undergreasing and equipment failure.
The GreaseBoss HME Solutions provide HME fleet managers with visibility and certainty that their critical assets are being correctly greased to maximise uptime and productivity.
key industries
we’re probably already overhauling yours…
GreaseBoss is revolutionising every major industry that relies on effective greasing solutions. By integrating advanced technology and innovative design into our greasing systems, GreaseBoss enhances equipment reliability and reduces downtime, ultimately driving productivity and efficiency.
Mining & Metals
Verify your machinery has been greased correctly, prevent unplanned downtime and reduce maintenance costs with GreaseBoss.
Manufacturing
With continuous and increasing demand for asphalt products from industry and government, keeping plant operating and drum mixers rolling is essential for both business and society.
Proven in the Toughest Conditions.
Trusted by the Best.
GreaseBoss versus Traditional Management
read more about us
latest news
Stay informed with the latest announcements, product updates,
and insights from GreaseBoss and the world of smart lubrication management.
got questions?
see our faqs
What training and onboarding do I get from GreaseBoss?
The GreaseBoss onboarding process is comprehensive and assists to set up the correct lubrication data in the GreaseBoss Cloud, and to prepare the site for installation, commissioning, and on-going operations.
GreaseBoss offers comprehensive training to customer teams in the field for installation, commissioning and hardware use, training for the office team on how to use the GreaseBoss Cloud, and how to interpret the reports & alerts.
Our operations are remote. If no access to 4G system are there alternative communication options?
Yes. The Gateway can be configured to use site WI-FI network or connected via LAN directly into the site OT network where the data is processed on an on-site server then forwarded to the GreaseBoss Cloud.
The GreaseBoss team will work with our customers to set up the most suitable backhaul option for client’s requirements.
How does my grease event data get to the GreaseBoss Cloud?
The data is synced from the devices to the Gateway via Bluetooth. The Gateway then forwards data to the GreaseBoss Cloud using the configured connectivity backhaul option.
Can I use my site wi-fi to connect to the GreaseBoss Cloud?
Yes, the GreaseBoss team will work with your site IT/OT team to use existing WI-FI networks to connect to the GreaseBoss Cloud.
Can I install or do I need a qualified GreaseBoss installer?
The system can be easily installed by customers with remote support from the GreaseBoss team but we do offer installation services directly with our Certified GreaseBoss installers to provide high–quality turnkey solutions to our customers.