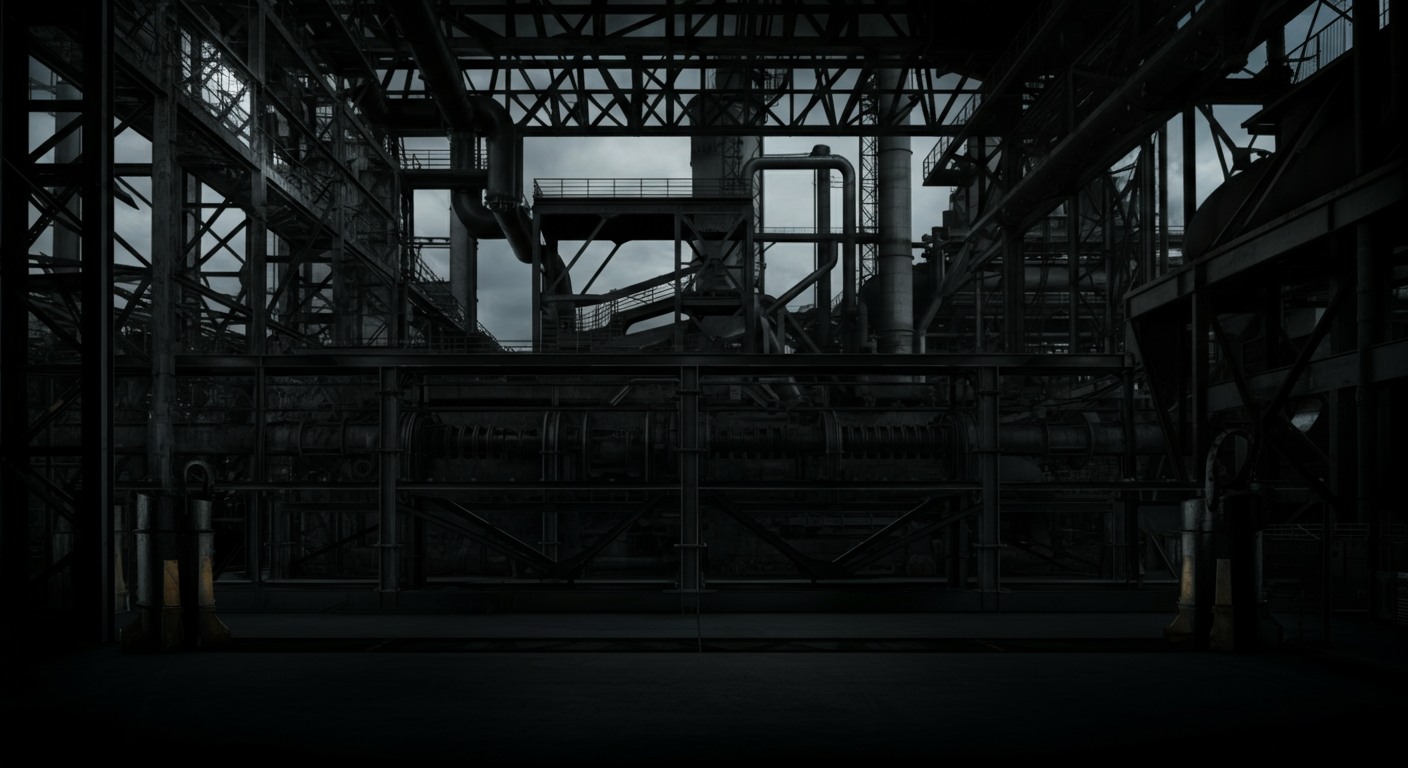
case Studies
Case Study
Komatsu Case Study
“The visibility of lubrication allows us to not only meet the operating targets, but extend the life of the machine” – Trevor Hyde, Komatsu‘s Regional General Manager, summarising the real-world impact of the GreaseBoss HME Solutions.
Learn why Komatsu trusts GreaseBoss for fleet reliability:
Case Study
Glencore mangoola – SYSTEMISE MANUAL GREASING TO BOOST RELIABILITY
The Mangoola team use external contractors to perform manual lubrication tasks and needed visibility and assurance that the greasing was being completed as per the lubrication schedule. The site was successful in:
- Gaining visibility and control over manual lubrication for both conveyors and electric motors.
- Systemising the manual greasing tasks to enable a new contractor to be greasing effectively within 2 weeks of starting on site.
- Monitoring of single point lubricator application volumes on critical pumps.
Case Study
EXCAVATOR BOOM FOOT & HOIST CYLINDER MONITORING -LIEBHERR 9600
The GreaseBoss monitoring system led to the detection of a bypassing injector on the swing box and an incorrect pump timer setting, resulting in estimated cost savings of $70,000 per year and prevented a potential swing box failure.
- Ability to detect bypassing injectors & incorrect pump timer setting
- Certainty over grease application volumes to critical points
- Cost effective critical point and lube system health monitoring
- Visibility and control over grease consumption
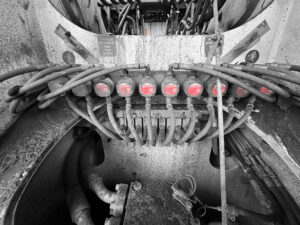
Case Study
EXCAVATOR HOIST CYLINDER AND BUCKET PIN MONITORING – KOMATSU PC7000
By installing Endpoint MP2s, the GreaseBoss system immediately identified a critical issue with the lube system pump, preventing a catastrophic failure of over $10,000,000.
- Greaseboss data revealed critical issue with lube system pump indicating a pump failure
- Verification of grease flow volumes and pressure to h-link
- Immediately detected a critical pump issue – preventing catastrophic equipment failure
- Provided visibility and certainty to maintenance teams over grease volume application
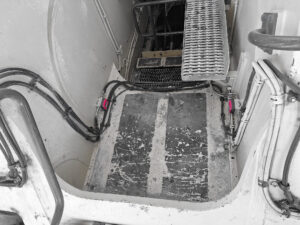
Case Study
HAUL TRUCK – CAT 796AC KINGPINS
This pilot saved our client around $6,000,000 a year. The GreaseBoss system immediately identified severe under-greasing across all monitored injectors, allowing targeted maintenance and significantly improved truck performance.
- Immediate identification of injector issues – all four injectors were severely under-greasing these critical components.
- Reveal root cause of greasing issue – many injectors were mistuned.
- Detected autolubricator system failure – this finding triggered a full fleet refit.
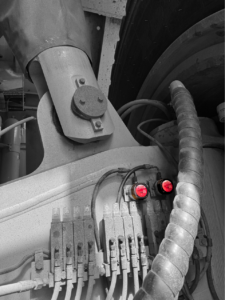
Case Study
HAUL TRUCK A-FRAME & Pump Monitoring
The customer experienced systemic A-frame bearing failures on their entire haul truck fleet. Without GreaseBoss, both trucks would have been operating with severe under greasing.
- Multiple major lubrication issues were identified on both haul trucks and reported to the maintenance team.
- GreaseBoss data showed 250+cc being dispensed each pump cycle – 5 times the expected amount.
- Detected incorrect pump timer setting.
- Highlighted erratic grease to the a-frame bearing.
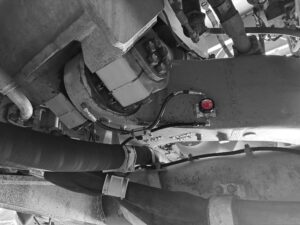
Case Study
Solving Haul Truck Kingpin Failures: $6.5M Annual Savings with GreaseBoss Monitoring
GreaseBoss’s monitoring system identified insufficient lubrication and systemic autolube configuration errors as root causes, saving our client around $6.5 million annually.
- Eliminate frequent and costly haul truck kingpin failures, saving $250k-$500k per event.
- Identify the root cause of lubrication issues, including insufficient grease delivery and faulty/mistuned injectors.
- Detect critical fleet-wide system configuration errors missed by standard checks.
- Achieve significant forecasted annual savings ($6.5 million) by preventing lubrication-related failures.
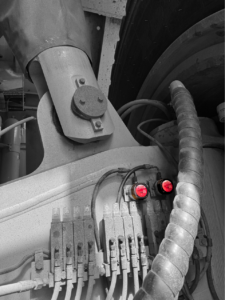
Case Study
Eliminating Costly Mining Sizer Bearing Failures with Precision Lubrication
- Eliminate costly grease-related bearing failures and associated production losses.
- Achieve exceptional ROI with $60m in forecasted annual savings from a $50k investment.
- Ensure precise lubrication with real-time data comparing planned versus actual grease volumes.
- Proactively detect equipment issues like failing autolube pumps before they cause major damage.
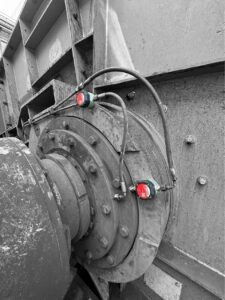